Our companies supply to Belarus, Russia, Ukraine, Bulgaria, Poland, Lithuania and other annular matrices and roller shells manufactured by GRAF GmbH (Raiffeisenstrasse 6, 68542-Heddesheim, Germany) for pellet presses of the OGM 1.5, OGM-0 brand , 8, GT-500, Munch RMP-520, etc.
The principle of operation of the ring die
Pre-crushed, homogenized material is fed into the matrix from the outside from above, enters the gap between the inner surface of the matrix and the rollers and is pressed into the holes of the matrix.
Under the action of the raw material continuously entering the granulation chamber, the material that has fallen into the holes gradually moves through them outward.
As a result of the generated pressure, the material is heated to a temperature of 100-120 degrees Celsius. At this temperature, the softening of lignin and other substances contained in the raw material or added specially (if necessary).
From the outside of the matrix, through the holes, ready-made granules come to the outside, which, subject to the technology of raw material preparation and granulation, have high strength and specific density of 1.1-1.3 (depending on the material).
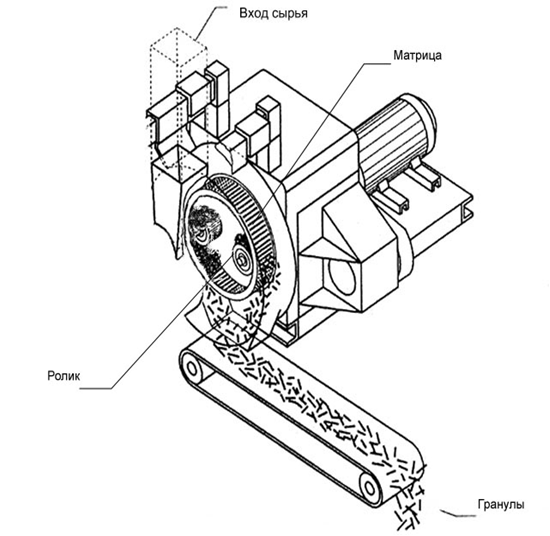
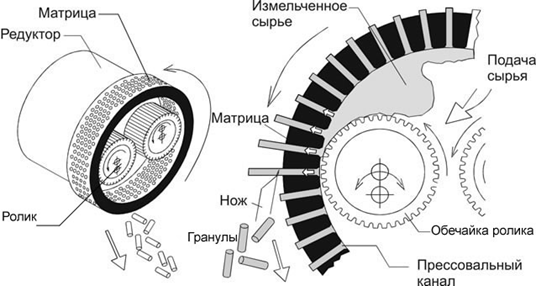
Offered dies with diameters of pressing holes 3.2 mm .; 4 mm., 4.7 mm .; 6 mm., 7.7 mm .; 8 mm., 9.7 mm; 12.7 mm; 19.0 mm are included in the set of a press for granulating mixed feed from grass flour, green mass, meal, bakery waste, etc.
The final product is used as feed for fish, poultry, pigs, cattle.
Dies, usually with a hole diameter of 6 and 8 mm., Can be used for the production of granular solid fuel in the wood processing industry.
Matrix description
The matrix is a large ring made of hardened special chrome-plated steel.
Through holes of a special shape are located along the diameter of the matrix.
On the side surfaces there are holes for attaching the matrix to the drive of the granulator press.
Depending on the type of pelleting press and the processed raw materials, the matrices differ in outer and inner diameter, width, number and diameter of holes.
– D = inner diameter
– B = overall width
– Pb = width of the pressing surface
– d = hole diameter
– Wd = wall thickness
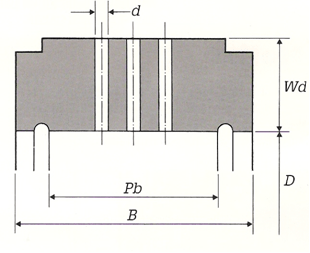
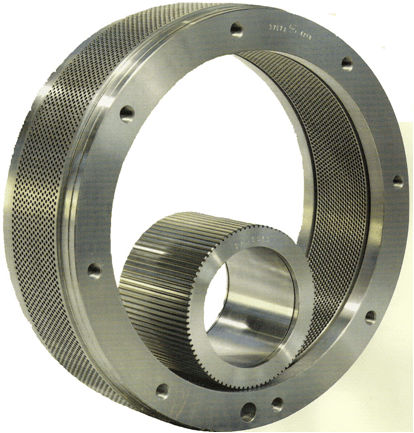
Matrix net weight: – OGM-1.5 – 129 kg., 132 kg .;
– GT-500 – 96 kg.;
– Munch RMP-520 – 161 kg ..
Packing: – wrapping paper and polyethylene film.
The main dimensions of the matrix for the OGM-1.5 granulator press are shown in the drawing:
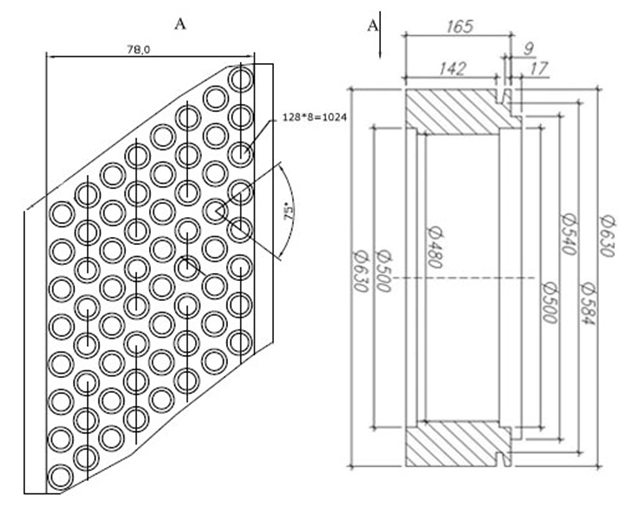
Roller shell
The roller (pressing roller), like the matrix, is included in the press kit for the production of granulated herbal, mineral and fish feed.
The complete roller consists of a shell rotating around an eccentric axis (shaft) on two roller bearings, which are pressed into the shell.
The roller is designed so that the raw material fed into the chamber of the granulator press is pulled between the rotating die and the pressing rollers (rollers) and pushed into the radial holes of the die, where granules are formed under the action of high pressure.
The roller shell is a steel ring.
The outer surface is made with longitudinal slots or uniform cylindrical grooves.
The inner part of the shell is machined for pressing the shaft with two bearings.
Roller shells are manufactured with outer diameters of 180, 190, 195, 220, 310 mm.
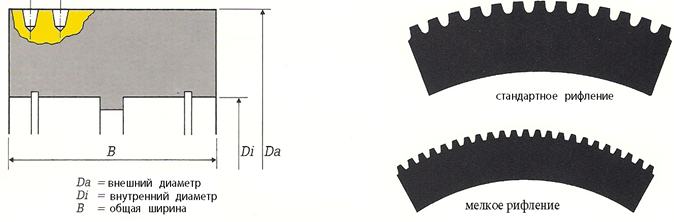
Dimensions of the roller shell for the OGM-1.5 granulator press in the drawing:
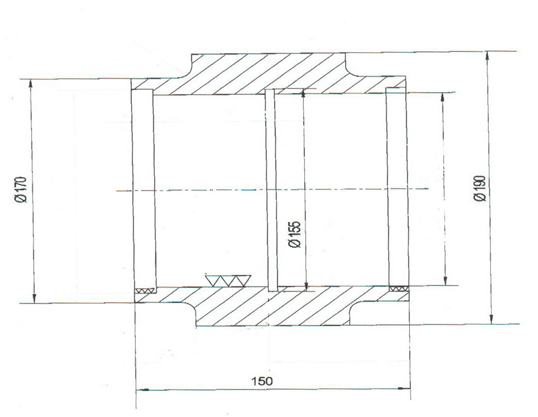
Shell net weight:
– OGM-1.5 – 9 kg.;
– GT-500 – 20 kg.;
– Munch RMP-520 – 21 kg.
Packing: – wrapping paper and polyethylene film.